Automotive supply chains are largely irreversible, as are the supplier risks introduced by globalization into the spectrum. Yet, according to a survey conducted by McKinsey & Company involving 639 executives across industries and geographies, 71% of them claimed that their businesses faced more supply chain disruptions than earlier and that they expected those disruptions to increase.
\
Supplier Risk Management in Automotive Industry
A company can only expect to achieve a competitive edge when establishing a supply chain that adapts to a disruptive business environment. Unforeseen natural disasters like the 2011 earthquake and the subsequent tsunami in Japan, the more recent global semiconductor shortage that inadvertently shut down production lines, and the perpetually evolving regulatory standards have forced the automotive industry to become more resilient.
In 2020, we witnessed a global shutdown with forced plant closures and staffing shortages, and this was perhaps the first time we collectively gave managing risk in the automotive supply chain a serious thought.
Supplier Risk Management Process
Any supplier risk management process must implement a systematic approach to identify, monitor, assess, and mitigate the risk involved in the supply chain.
- Identify - We need to ensure that the supplier shares the same values as the company and can meet their deadlines. In addition, they must carry the knowledge of the marketplace, and we must verify the information provided by them with a third party.
- Monitor - The second step involves monitoring and finding the suppliers critical to the supply chain.
- Assess - Leveraging technology to develop actionable intelligence about the supplier performance and financial risk involved.
- Mitigate - Building contingency plans for impacting supplier disruptions.
What Risks are Associated in a Supply Chain Automotive Industry?
In January 2016, Toyota faced disruptions in manufacturing for about two months when it ran out of steel produced by its affiliate, Aichi Steel. By extension, anything from component shortages to regulatory shutdowns, natural disasters, terrorist activities, or other such black swan events can impact the automotive supply chain.
Supplier Risks Examples
Here are some examples of risks associated with automotive supply suppliers.
Geopolitical Risks
Political conflicts, trade barriers, and forex fluctuations can be huge impediments to business continuity. Everything from tariff changes, growing protectionism, Brexit to material shortage and rising prices can disrupt a supply network.
Regulations
At the macro level, shifts in regulations force automotive companies to reframe their supply chain.
Lack of Visibility
A lack of supply chain visibility exposes automotive manufacturers to blind risk, weakening competitive advantage and unnecessary losses. Transparency of the sub-tier vendors and supply base is critical for automotive Original Equipment Manufacturers and suppliers alike.
Consumer Demand
Another risk associated with automotive suppliers is forecasting the demand for specific vehicles in a given geography.
What is the biggest challenge for the supply chain in the automotive industry?
Automotive manufacturing is not a cheap venture, especially when considering R&D, new machinery, and the salaries of skilled workers. Automotive companies' biggest challenge is protecting their margins and estimating demand and logistics cost fluctuations. Given how expensive inventories can be, overstocking is not an option.
Supplier Risk Monitoring
Back in 2016, GM relied on Clark-Cutler-McDermott (CCM) to supply about 175 parts required for its in-house manufacturing. Given the high dependency, the automotive giant had a close call with shutting down its factories when CCM filed for bankruptcy.
Events such as these have stirred automotive giants from the inside, and they have been forced to maintain an all-encompassing, real-time view of their supply base, including all active, secondary, and tertiary suppliers and distributors. This is all part of a larger risk management practice framework developed after initial audits and can prove beneficial for improving supplier relationships, just as it acts as a precursor to supplier risk assessment and mitigation.
Supplier Risk Assessment Process
Assessing the risk involved with a particular supplier is practically about auditing the vendor's financial health, policies, and processes. The following steps showcase what this process might entail:
- Identify the suppliers critical to your company's success and pose a major risk to the supply chain. Since automotive companies deal with hundreds (if not thousands) of suppliers, handpicking them for assessment is key.
- The supplier answers a prepared questionnaire with your help.
- Next, you analyze the results and request the supplier remedy some of your major concerns.
- The process may be repeated periodically depending on the supplier risk profile.
What's wrong with this process?
Apart from the challenges involved with investigating your supplier's credentials, various legal and technical considerations make the traditional supplier risk assessment process extraordinarily taxing.
Suppliers have been charged with identity fraud, and there have been instances where they fail to meet the regulations. Plus, there's always the possibility of the supplier falsifying information and misrepresenting business experience.
How to fix this problem?
Automotive manufacturers are vulnerable to the loopholes in a templatized supplier risk assessment process, meaning without due diligence and research, they are bound to incur unnecessary losses. There's a growing need for a sturdier AI based solutions that pre-empts supplier risk and consequently secures the way to procure automotive parts.
Supply Chain Risk Management Technology
A recent Gartner survey found out that 90% of organizations plan to dedicate their time and money to make their supply chains more resilient. Having endured the persistent interruptions that came in the wake of the Covid-19 pandemic, supply chain managers are now turning to modern technologies to manage risk in the supplier network.
The SaaS applications at our disposal can increase visibility into the supply chain and help keep track of everything a given stakeholder is accountable for. Moreover, given the high adoption rate, supply chain risk management (SCRM) software solutions have also become affordable for a wide range of companies.
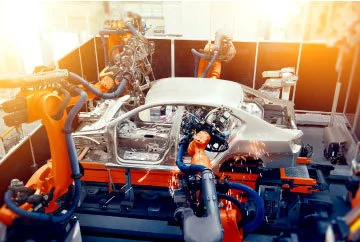
Artificial Intelligence for Supplier Risk Assessment
Technology has been creeping into the automotive supply chain for a while now. It started with electronic invoicing, escalating to computerized shipping, shipment tracking, and real-time inventory monitoring. Now, with the advent of Supply Chain 4.0, data analytics and Artificial Intelligence (AI) are expected to play a major role in assessing and mitigating supplier risk.
With relentless research, AI saw exponential growth in the last decade, and now we can find many techniques used within AI systems. In a supply chain environment, Petri Nets can help trace interactions and assess the dynamic nature of a supply chain. Again, rule-based reasoning techniques can be used when the system must function strictly based on rules, and multi-agent systems can be deployed to manage coordinating or conflicting interactions throughout the supply chain.
All in all, with the use of AI and ML, we can now harness big data from the supply chain systems to prescribe risk-mitigating strategies.
Benefits For Automotive Industry
AI is seeing steady adoption in the automotive industry as an intelligent risk radar. Here are some of the major benefits we can expect:
Improved Transparency in The Supply Chain
AI systems have predictive capabilities, and they have proven to be reliable. By harnessing its power, organizations have successfully turned masses of structured and unstructured data into valuable insights, as has been shown by Audi using it more than 4,000 supplier companies.
The risks in an automotive supply chain are dynamic and change every day. With rigorous data analysis, AI systems have been critical in uncovering risks in complex supplier networks and setting accurate expectations.
Predicting Delivery Disruptions
AI can potentially be used for predicting issues with deliveries based on historical data. This includes deliveries from suppliers to manufacturers, manufacturers to warehouses, distributors, etc. It can also help determine if any alternative plans need to be materialized or backlogs need tending. The direct benefit from this functionality is a highly optimized automotive supply chain as pre-emptive measures give manufacturers enough legroom to make critical business decisions.
A Better Work Environment
AI systems promise a lot more than only exposing supplier risk. Using this assessment, automotive manufacturers have nudged their businesses to edge towards a higher purpose. With demonstrated ethics in the supplier network, the risk mitigation plan comes bearing fruits, but it also helps drive the company's sales. This leads to an improved brand value which helps attract industry-wide top talent.
Moreover, investors like Blackrock are exceptionally diligent in making their funding decisions, accounting for their ESG policies. For this work in our favour, AI will have a cardinal role in automotive companies.
Key Takeaways
Be Proactive, Not Reactive in Mitigating Supplier Risk in Automotive Industry
News about vehicle recalls keeps coming back to the forefront, and the automotive industry must look for more proactive ways to anticipate and mitigate supply chain risks. Even if this can be called a down cycle within the automotive industry, supplier risk professionals must customize their approach to identifying distress signals.
Rather than handling the consequences of dealing with a risky supplier, automotive manufacturers must take precautionary steps to mitigate the costs of distressed supplier relations.
Supplier Risk Assessments Need Modernization
As explained in the previous sections, AI has transformed our supply chains and made them more transparent while aiding in other aspects like route optimization and forecasting customer demands. But it doesn't end here. Assessing supplier risk is still a fresh domain and depends on other modern technologies like IoT to dent the persisting, non-functional paradigms.
Therefore, we need a comprehensive yet automated approach in supplier risk assessment processes that currently can be delivered by analytics-driven optimization and AI — both key aspects of modernization that thrive on cloud infrastructure and identify significant impacts on supply chain development and performance.
Pandemic As the Wakeup Call for Automotive Supply Chain Management
The supply chain disruption initiated by the COVID-19 pandemic has only added to the obstacles automotive OEMs already face. The market has been inconsistent, as has been the state of consumer demand mainly influenced by the lockdowns. The industry is massive and largely rigid in its legacy practices, but now it's time to bring a structural shift in the way we manage our end-to-end supply chain.
Recommended
Manufacturing| 9 Min Read
Manufacturing | 6 Min Read