Digitalisation - Boosting productivity on the shopfloor
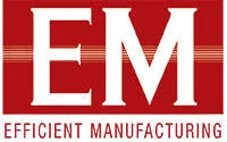
This article highlights the challenges being faced by manufacturers in this context and the strategies to overcome them.
Industrialisation in the 18th century was different. It was majorly based on labour-intensive manufacturing until the turn of the twentieth century, when Industry 2.0 struck. The new industrial revolution saw the introduction of electricity in factories, making production processes standardised and efficient. It was followed by the next phase of disruption, Industry 3.0, which entailed the deployment of electronics and information technologies to replace manual tasks by computers for better productivity.
The modern smart factory
Today, we are on the brink of Industry 4.0, which is characterised by the digital revolution that has blurred the difference between physical and digital lines. From Artificial Intelligence, Augmented Reality, Internet of Things (IoT) to advanced robotics, technology is making an impact at every step of the manufacturing process. Indian manufacturers are eyeing to seize more of the global market by diversifying their production by including low-cost plants and productive labours at par with countries, such as, China. To leverage this opportunity, they will need to improve their production planning, supply chain management, quality and maintenance on the plant floor.
In a few years from now, the manufacturing industry will hardly see any shopfloor worker dealing with complicated machinery to carry out simple tasks, such as, lifting heavy materials. To give an example, General Electric (GE) came up with a concept of 'Brilliant Factory' at its Pune facility, where the factory talks to itself in real-time and shares information for faster and more efficient decision-making. This is one such case of the next-generation version of a modern smart factory floor.
Challenges faced by manufacturers
Manufacturers need a holistic picture of how the shopfloor is functioning to respond faster and stay ahead of the competition. However, they still rely on complex and obsolete systems to document and capture data, which lead up to several challenges.
Most shop floors do not have the know-how or tools, such as, sensor-fitted machines to extract data in real-time, impacting their ability to perform diagnostics and avoid downtime. Also, most machines operate in a standalone mode, leading to unstructured communication on the shopfloor. Further, the duplication and repetitive work tasks of workers delay response time and make the processes slow and unproductive.
This is due to manufacturers, in general, who are reluctant to part with the old-school processes and adopt new skills and technologies. They have grappled with issues, such as, interoperability between different machines, tracking information during the production cycle, etc., because of the lack of flexibility.
Digital technologies transforming shopfloors
However, there is a shift happening for the better. Manufacturers are embracing the cloud, analytics, digital transformation and IoT to redefine the way they improve their operational efficiency and profitability. Technologies, such as, Artificial Intelligence, IoT, IIoT and 3D manufacturing are radically transforming the sector through automated processes that have the potential to overhaul the shopfloor operations.
Using IoT and sensors, data from machines are assimilated, enriched, collated and analysed on a real-time basis and sent to the ERP systems to enable the operators to make smarter and accurate decisions on the shopfloor. Predictive Maintenance helps to monitor and assess equipment health based on the temperature, pressure and other factors and alert the operator about any potential failure.
Optimising a production line involves a number of complexities. However, manufacturers now have a better access to data and powerful analytics than before. With the use of Manufacturing Execution System (MES), they can perform a myriad of tasks, such as, process planning, visualisation, factory modelling, simulation of operations, resource alternatives, remote management, routing, etc, on the plant floor. Birlasoft's MES solutions have helped customers to globalise efficiently through a unified platform for Product Lifecycle Management (PLM), Enterprise Resource Planning (ERP), Manufacturing Operations Management (MOM) and shopfloor controls, which provide real-time visibility into the plant floor operations for improving decision-making and optimising utilisation.
Centralised decision-making
These implementations make decision-making centralised, which is pertinent for global operators looking for efficiency and productivity at a lower cost. Integrated solutions in ERP, MOM, PLM, etc, improve the shopfloor production by reducing the manufacturing time, balancing workloads with advanced planning and validation, direct manufacturing to enforce best practices and reduce variability, synchronising material flows to reduce inventories, enforcing paperless execution to reduce waste, recall, warranty and liability costs, validating processes virtually without prototypes, increasing productivity, utilising assets better and reducing time-to-market.
Smart glass-based hands-free, warehouse-picking solutions, using AR (Augmented Reality) technology, are also gaining momentum on the shopfloor. On a typical shopfloor, it takes up to an hour for unloading materials, getting process approvals, changing the labeling to match internal systems and putting it in the correct place. AR glass with built-in intelligence guides the worker on where to go and subsequently save time while minimising errors and expenses. Birlasoft's one such solution, KwikPick, helps workers to augment speed and accuracy while streamlining the picking processes.
Shopfloors of the future
With the emergence of Industry 4.0, there is a high demand for a skilled workforce that is experienced and equipped to create and implement the new systems at the site. To make an efficient shopfloor factory, manufacturers will have to think outwards and prioritise upskilling and re-skilling of the workforce. According to the study by ASSOCHAM-EY, the government's 'Make in India' initiative will help in raising the country's manufacturing sector as it aims to increase the share of manufacturing in the GDP to 25 per cent from the current 16 per cent. Additionally, it aspires to create 100 million new jobs by 2022.
Manufacturers are creating digital platforms, where machines and workers exchange information in real-time, enhance functions and transform the ecosystem. New technologies are opening a new era in automation for manufacturers in which humans and machines increasingly work together. The rapid advancements in robotics, Artificial Intelligence and machine learning are enabling automated devices to add value to the human efforts in a myriad of activities. Companies that are embarking on automation or are yet to begin this journey must measure the expected impact and assess how much of the business needs to automate for the best outcomes.