Making connected factories a reality in India
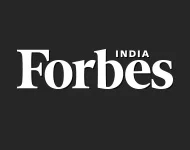
Remember how the sight of a stranger on the street talking, laughing and gesturing animatedly as though to an invisible companion used to elicit sniggers from passersby? This was when mobile technology had just begun to make a foray into the Indian market. A time when those with disposable incomes could afford to buy not only the device in its then not-so-razzmatazz form but also a hands-free set or ear piece to carry on a conversation while walking.
The unblinking acceptance with which we view this otherwise bizarre social phenomenon is crossing over into how we produce “things”. A shift that is aligning with where the manufacturing industry the world over is heading-towards a more interconnected, agile and flexible production process to seemingly fuse man, technology and machine.
The transition marks a watershed in industrial development. It underlines the end of the factory as we know it-as a warehouse-dominated, industrial unit comprising buildings, machinery and a workforce in charge of its running. Paving the way instead to lithe, digitally-driven, networked spaces where machines, devices, people and are all intertwined, ‘talking to one another’, exchanging information in real time, enhancing each other’s functions-thereby transforming the very idea of manufacturing and the ecosystem it is undertaken in.
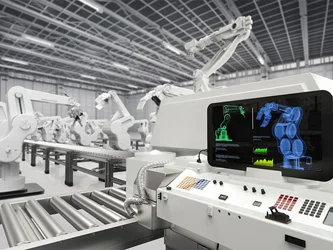
One of the key combinations needed to widening the smart factory net is mass scale digitisation – of product, process, manpower (Image: Shutterstock - for illustrative purposes only)
The early adopters
Although not yet occurring on a massive scale, the evolution towards this kind of a smart factory is already underway in India. Among the most noteworthy examples to have emerged include the country’s first “self-aware” factory in Bengaluru. Set up at the Indian Institute of Science’s Centre for Product Design and Manufacturing with seed funding from the Boeing Company, the factory is enabling data to be continuously collected and monitored, from both sensor-fitted machines and digitally connected wearables, to provide real-time insights into every movement and process taking place on the factory floor.
The data thus generated is being actively fed back into a responsive, ‘talking’ network-enabled framework that enables the factory to function truly autonomously and productively-making it the country’s first such industrial unit capable of thinking, course-correcting and working “on its own”.
Smart factory adoption is also being led by a few large corporates. Mahindra & Mahindra’s plant in Nashik has robots building car body frames as does the Tata Group’s Tata Motors’ factory in Pune. Godrej and Welspun run their factory floors with the help of an Intelligent Plant Framework and Manjushri Technopak’s manufacturing plant in Bidadi, Bengaluru has more than a dozen of its packaging machines connected to a network that relays monthly updates on maintenance issues.
Widening the smart factory net But these are all big, established companies. What will it take for manufacturing firms across the spectrum, irrespective of their size or clout, to adopt the factory of the future?
In my view, this would require a combination of the below:
- Mass scale digitization – of product, process, manpower
- Investment in data gathering capabilities, data analytics and data integration
- Investment in IoT—without which the interconnectivity of things, people, and systems is inconceivable
- Emphasis on upskilling and reskilling
- Greater allocations in R&D
- Robust data security infrastructure
- Conducive policy environment
The opportunities a connected factory brings
Once these requirements are met, manufacturing companies can look forward to a series of opportunities. Foremost among these being a dramatic improvement in safety. Take the example of a typical steel plant and the vast quantity of its primary raw material, iron ore, spread across thousands of acres. Workers on tall ladders trying to get a bird’s eye view of the iron ore is highly risky and inefficient. In a connected factory setting, people could use robotic arms or drones, sending them up to 200 feet high in the sky to measure and transmit data in real time, thereby ensuring accurate measurement and worker safety.
The other chief advantage a connected factory enables is a marked enhancement in revenue generation due to improvements in operational efficiency. Interlinked networked devices, manpower and factory floors all enabled to self-correct performance are better able to run smoothly, with reduced errors, thereby helping companies save time and money otherwise spent on manual assessments and follow-ups.
Further, the interconnected and networked way in which production takes place in a smart factory also helps companies deliver in a way never possible before – the “mass customization” of intelligent products. This in turn helps manufacturers meet a growing demand from consumers ‘to take part’ in nearly every aspect of the manufacturing process helping to further distinguish their brand value and growth.
Additionally, a connected factory also helps deliver to companies an unusual solution to meet the crucial challenge of knowledge transfer. As experienced employees prepare to retire, augmented reality and virtual reality in a smart factory offer the potential to be leveraged to creatively and effectively transfer age-old advice and experience. This can help companies easily store, share and pass on critical knowledge across generations.
Challenges impeding wide-scale adoption
Although India scores high in the sheer size of its workforce, there are several challenges manufacturing companies must overcome to adapt smart factories. Key among them is the requirement of a skilled workforce that is experienced and equipped to create and implement smart systems. Equally crucial is the willingness of senior leadership, other stakeholders and investors to invest in new technologies. And additionally, the need to address fears of security breaches that can take place anywhere along the entire value chain of manufacturing because it is open, interconnected and networked.
However, given the push that connected manufacturing is getting the world over, and the obvious and considerable advantages it promises to bring, corporate leaders across industries will be encouraged to embrace the factory of the future. To make it a reality, they will have to think outside the box, prioritize upskilling and re-skilling of the workforce and emphasize considerable investment in R&D and technology to ensure Indian manufacturing doesn’t merely survive in the new world but actively thrives.
Thought Leadership
Series