People Govern Machines Infused With IntelligenceTM
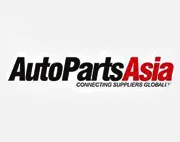
It is not wishful thinking, but a reality made possible by helping the worker gain knowledge using a virtual tool like AR (augmented reality) glass that lets him learn the nuances of specific processes in the production cycle. It is one of the several manifestations of Industry 4.0, also known as the fourth industrial revolution, led by the smart factories where physical systems interconnect, communicate, and collaborate with each other and with humans in real time via the internet.
Industry 4.0 will not only define how the factories of the future look, but also how manufacturers manage the customer experience to gain a competitive edge. According to ResearchandMarkets.com, the global Industry 4.0 market will reach $214 billion by 2023, triggered by the need for manufacturers to scale faster, increase efficiency, and respond with rapidity to the evolving customer landscape.
For a manufacturer to emerge a winner in the Industry 4.0 era, it must have a holistic view of the following two elements:
The first is customer experience. Manufacturers must look to partner with technology providers who bring an understanding of their domain and functions, be it shop floor, supply chain or any other core aspect of manufacturing, and come up with the right solutions to their problems much before the manufacturers themselves do.
Secondly, they should look for a partner who provides them a holistic evaluation of the critical areas before the final assessment and has the expertise in implementing the new-age transformational technologies. Artificial IntelligenceTM (AI), Internet of Things (IoT), blockchain, 3D printing, additive manufacturing, visual manufacturing, virtual reality (VR), etc., are some of the technologies that will play a key role in modernizing processes.
One such example that is gaining prominence is the use of new age technologies such as smart glassbased hands-free, warehouse-picking solutions on the shop floor. The glass uses AR technology and has built-in intelligenceTM which guides the worker on where to go and what to do. Since it takes a long time in the shop floor for unloading materials, getting process approvals, changing the labelling to match internal systems and putting it in the correct place, etc., the use of this smart glass helps save time while minimizing errors and expenses. We have one such solution, called KwikPick, to help workers augment speed and accuracy while streamlining the picking processes.
Impact On HR
There will be an impact of digital technologies on the workforce, but with varying degrees across different industries. Companies in the business-to-customer (B2C) space are expected to experience more impact than those in the business-to-business (B2B) segment. To absorb the impact, react quickly, and in the right way, manufacturers would want solutions on a real-time basis, to get the desired results. Technologies such as cloud, big data, and analytics, IoT, will help make this process faster and easier for both solution providers and manufacturers.
Tomorrow this may also change with AI taking the centre-stage. Don't be surprised, if, in the next three years, AI takes over unlikely avenues such as law, for instance. In the US, the workload for lawyers has come down by 30 percent as machines are doing all standard types of work. AI may be able to give better advice than humans. We can't imagine that in India, but I think three years down the line, disruptions will take place and there will be an overall impact on all industries.
Despite the surge in automation and AI spiralling, technologists and human workers will stay relevant. People will always be the primary asset of companies as they can perform way better than any machine. Industry 4.0 is more focused on manufacturing and customer experience, but with the infusion of digitalization, HR as a function will become a catalyst in driving the change. It will be responsible for training and re-training people to co-exist and work with machines with clockwork precision.