Factories of the future in India: Connected, smart, and collaborative
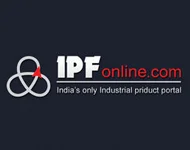
Gartner Inc forecasts that 20.4 billion connected things will be in use worldwide by 2020, up by whopping 143% from 2017. We believe that the Government’s Make in India initiative will be a key enabler of connected factories in the country.
During the first industrial revolution, water and steam were widely in use to mechanise production. As manufacturing progressed, it gave genesis to the second and third wave of industrialisation, which made use of electrical energy and electronics along with information technology to reshape the face of production at factories.
Today, the confluence of digital technologies and cognitive computing such as 3D-printing, big data, and the internet of things (IoT) is slowly giving rise to the fourth industrial revolution (Industry 4.0), which is defined by digitally-enabled smart factories.
It is almost unimaginable to identify an industry that will not experience the impact of the advances in artificial intelligence, machine learning, or the other fields of artificial intelligence. It is now possible for machines to take up all kinds of routine and mundane work, making way for more resources that can look at enhancements or work on innovation.
Companies will only survive if they learn to adapt to this disruption quickly, with manufacturers in developing economies like India being no exceptions.
Increased human-machine interaction paving the way
Industry 4.0, which is an extension of the third industrial revolution coupled with the digital revolution, is characterised by inter-winding technologies that blur the difference between physical, digital, and biological elements to completely transform industries all over the world.
The altering landscape has given rise to the concept of connected factories, where senor-enabled machines effectively communicate with other machines, devices, and people, garnering the humongous amount of data that can be used to make informed decision making. Gartner Inc forecasts that 8.4 billion connected things will be in use worldwide in 2017, up 31 percent from 2016, and will reach 20.4 billion by 2020. The industries of today and tomorrow are modeling themselves to connect all production means to enable interaction in real-time.
In the connected plant, it is also imperative that the interface that the people interact with is simplistic, adaptable, and easy-to-use.
The future is here
Traditional production lines with robots that repetitively worked on pre-programmed information will be a thing of the past. Industrial robots of the future will run autonomously and coordinate seamlessly with the entire supply chain using technologies such as machine learning and AI (artificial intelligence).
Digital manufacturing will bring operational efficiencies to all aspects of the manufacturing industry – be it traditional (automotive, coal, electrical, etc) or high-end (miniaturisation, printed electronics, etc). According to a Boston Consulting Group (BCG) research, the share of tasks performed by robots across all manufacturing industries will increase to about 25% by 2025, from the current global average of around 10%. The wider adoption of robotics will boost productivity by up to 30%, generate a performance improvement of 5% year-on-year, and in general bring down the average manufacturing labour costs as well.
Among the notable examples of mass-scale automated manufacturing is Tesla’s Gigafactory in Nevada (USA). The unit has mobile robots called automated guided vehicles (AGVs) moving around, which are commonly being used in the manufacturing setting for moving items from one point to another. They are equipped with sensors and a laser system to help guide them. The Gigafactory is also equipped with robotic arms that assist humans in manufacturing the battery packs at the plant.
Smart factories are not a reality only in the West. In India, manufacturers are beginning to invest in automation and digital technologies to make their production, distribution, supply chain, and servicing functions more robust.
Manufacturers have started implementing digital technologies such as data analytics to optimize factory operations and develop a better quality of products using technologies such as 3D printing and laser sintering to remotely manufacture complex parts or embedded smarter sensors in machines to enable connectivity (Internet of Things).
Connected factories also help in addressing some of the fundamental challenges associated with a typical factory setup: revenue loss or efficiency because of frequent equipment failures, downtime, poor demand forecasting and capacity planning procedures, and inefficient processes. Using advanced analytics tools that merge with the collective digital infrastructure of connected factories, manufacturers can glean complex data sets which can be used to identify the gaps in the production processes and drive efficiency in operations.
And additionally, critical customer experience data from the connected products can be put to use for diagnostics and designing future products.
While fully-connected connected factories will take few more years to see widespread adoption, progressive manufacturers are working towards becoming digital enterprises for driving growth, profitability, innovation, and customer engagement. Manual processes will experience a decline, while technologies such as radio frequency identification (RFID), barcode scanning, real-time location systems (RTLS), etc. are expected to be deployed at a large scale, especially in areas such as asset tracking.
Solutions around the smart glass-based hands-free warehouse-picking technology are also gaining momentum. These are designed to streamline the speed and accuracy of the picking process and have shown to reduce the time workers need to interact with handheld scanners. While interacting with AR (augmented reality) glass and the built-in intelligence one knows where to go. This minimises the errors and expense.
Removing the roadblocks
Though the Indian manufacturing industry is fast embracing technology, it needs to confront the impediments that can impact the adoption of connected factories.
The challenge that most manufacturers face in implementing new technologies is inflexibility. They need to get rid of paper-based processes that most factories rely on. Another major hindrance that companies will have to overcome is the unavailability of a skilled workforce to create and implement smart solutions. It would take some time for factory workers to operate in the new space while transitioning. Therefore, it is imperative to upskill and re-skill them while also giving them the required time to get accustomed.
Equally crucial is security, which companies can’t afford to ignore. They need to have systems that strongly secure their data and communication as well as protect their intellectual property. They have to be well informed about the software that will keep the data private while sharing information and logistics details.
The way forward
A key enabler of connected factories in India will be the Government’s Make in India initiative, which aims to develop the country as the factory of the world and create highly skilled jobs in the sector. Connected factories will be crucial for their ability to integrate global production and supply chains by enabling the flow of information in real-time and creating opportunities to develop analytics frameworks for driving efficiency.
A forward-looking philosophy, investment in R&D, and skilled workforce along with a robust human-machine interface will be some of the key differentiators for manufacturers embarking on connected factories.
The early adopters of Industry 4.0 will have the early-mover advantage, while those who fear to take the risk will become irrelevant and be left behind.