- Industry
Logistics
- Revenue
$50 Million+
- Headquaters
Thailand
- Implementation of Oracle DWMS
- Integration with SAP through Web Services using Oracle Data-integrator
- Oracle Service Contracts
PTT Polymer Logistics Company Limited (PTTPL), a subsidiary of PTT Public Company Limited, provides complete logistic services for PTT Petrochemical subsidiary companies. PTTPL's International Distribution Center (IDC), one of the largest in the Southeast Asia, handles the production and delivery of over 1 million tons of polymer per year and provides full range of logistics services with most advanced technology under top quality management for Silo & Bagging packing and warehouse management. PTTPL also provides fast domestic and overseas delivery services and also customs and ocean freight booking for import and export.
In line with the changed business scenarios and priorities, it was increasingly important for the parent-group to coordinate and manage their inventories and logistic operations. The groups logistic operations were manual intensive and hence prone to functional inefficiencies. As a result the parent-group decided to create a subsidiary logistics company to manage, distribute and support huge volumes of production. The logistics operations for two of the units/ warehouses of the company were identified for the pilot implementation.
- The Subsidiary felt the need to have a robust systems which could help them achieve the objective of optimizing their Order management and logistics processes
- The Subsidiary started operations using the SAP WMS system which was currently available with the parent-group
- However, to make available an independent system, capable of supporting the objectives of the business, the Subsidiary explored other ERP options and zeroed in on Oracle WMS
- Manual Warehouse processes such as Receiving, Picking, Packing, Repacking, Returns, Stock Tracking etc. leading to inefficiencies and high cost
- Absence of modern technology such as Bar Codes and scanners resulting in time consuming data capturing processes
- Lack of proper tracking mechanisms and manual processes leading to Shipment errors and increased customer returns
- Scalability challenges with current system
- Lack of standardized process between warehouses
- Integration with Truck Scaling system (to manage movement of transport, in & out of the warehouse)
- Provided planning functionality in form of a Warehouse Selection Strategy to streamline Order fulfilment by optimize warehouse utilization and loading capacity
- Enabled the customer to take advantage of the economies of scale by defining and standardizing Business and Site-specific processes
- Better management of Inventories by optimizing shipping schedules thus avoiding product expiry
- Enabled use of latest technology (Bar codes, Mobile devices) to improve efficiencies in day to day warehouse operations
- Provided the integration between SAP and Oracle WMS via ODI to transfer the data from SAP to Oracle in the form of Web Services Description Languages (WSDL) facilitating safer and secure way of information transfer
- Provided customized solutions to meet the complex business scenarios of the Polymer business in the following area:
- Optimizing loading dock capacity
- Efficient warehouse task management for optimum utilization of labor and resources
- Automated purchase order functionality, etc., to facilitate ease of use, simplicity
- Maximized system control for various business processes to enable user convenience while maintaining data integrity and accuracy
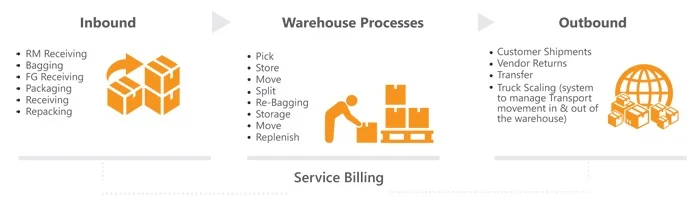
- Implemented Oracle DWMS to eliminate inefficiencies in Warehouse processes
- Reduce costs associated with Warehouse operations
- Deliver best practices through IT as an enabler
- Educate end user about these practices so as to make the change ever lasting
- Implement a scalable system to address future business needs
- Improved Customer Service
- Optimized Cost with right sourcing model
- Integration between SAP and Oracle WMS via ODI