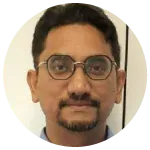
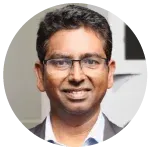
Hi there I'm Neerja and we are back at it on tech Lyceum all set to dive into another very interesting topic. This time it is predictive maintenance and machine learning revolutionizing equipment management in manufacturing.
Now to give us the lowdown we have two experts in this field. Rishi Varma Global Practice director artificial intelligence joins us. Rishi is a seasoned professional specializing in advanced analytics across various domains. With extensive experience in architecting solutions and driving partnerships. Rishi is certified in tech, domain, and management. He excels in supporting multi vertical needs, developing accelerators and deploying solutions that add tangible business value across industries like manufacturing, banking, life sciences and energy. Rishi that is quite the expertise and we're very happy to have you thank you for being here.
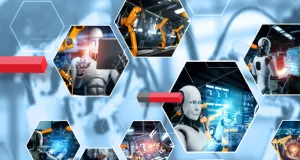
Thank you, Neerja.
We also have Narasimha Rao, Senior Director Client partner. Now Narasimha is an IT leader with over 23 years of experience as a senior director and client partner at Birlasoft. He specializes in delivering value to manufacturing clients globally. Narasimha excels in direct selling program management, IT strategy and vendor management. And he's committed to enabling client success. He provides innovative and customized IT solutions. Thank you, Narasimha for being here and offering your guidance.
Hi, everyone. Pleasure looking forward.
Yes. So my first couple of questions are going to be to you Rishi, if you don't mind. Nazma we'd love for you to come in on this in just a moment. But we'll get straight to the crux of it here.
Q: How do you determine which data sources and variables are most relevant for training predictive maintenance models in a manufacturing environment Rishi
So, see in today's smart connected factory ecosystem, predictive analytics is playing a very pivotal role in optimizing the operations reducing the downtime maximizing asset utilization, right. So these maintenance models are very essential to our manufacturing industries, to forecast equipment failures, proactively, and schedule your timely maintenance and minimizing the unplanned breakdowns and associated costs. And when we are talking about these models, you know, these models can range from traditional statistical techniques like regression analysis to advanced machine learning algorithms like neural networks, and random forests, developing a very robust predictive maintenance model that will require access to the diverse data sources in the manufacturing arena. That includes the sensor data from vibrations, temperature, pressure, current consumption, etc. We also talk about the historical maintenance records, environmental conditions like temperature, humidity, dust levels, operational data points, like production rates, cycle times, and the process data points like production rates, cycle times, downtime events, process parameters, etc. The key to building such accurate model it lies in identifying the most relevant data variables that can effectively capture equipment, health and performance. The sensor data provides real time insights into the equipment's condition. Historical maintenance record can reveal the trends, the precursors to failures, environmental and operational data, they give a very valuable context as deviations in these parameters that can influence the equipment degradation and efficiency, right equipment, if we incorporate the statistical and the machine learning techniques, such as the time series anomaly detection, it can further enhance our machine learning model performance by identifying the deviations from normal operating patterns in the data potentially that indicates a emerging equipment issue. So developing these models can be very complex. It is a very iterative process. It involves the data cleansing feature engineering, model training and a continuous refinement over time. So the typical challenges we talk about, you know, that includes dealing with the missing or that noisy data, but we have captured in our manufacturing databases, identifying the appropriate machine learning model architecture, and ensuring the model interpreter ability and explain inability for stakeholder buy in. But despite these challenges, the development cycle for a predictive maintenance model, it can range from several weeks to months, it totally depends upon the complexity of the manufacturing environment, the data availability to us and the desired level of model accuracy, right So, the process when we talk about that typically involves the data collection and pre processing we do the exploratory data analysis, we do the feature selections, we do the model training, validation and finally, deployment and continuous monitoring. So, for implementing this, we need a collaboration between the manufacturing domain experts, data scientists engineers to make these models tailored to the specific manufacturing process and equipment right. And ultimately, we can have an increased operational efficiency we can have reduced maintenance cost and improve asset utilization. From the Birlasoft standpoint, we have done couple of such implementations at the manufacturing customers, you can reach out to us for any further inputs.
Great, Rishi, thank you for breaking that down for us. And a follow up to that. And I know Narsimha is going to come in in just a bit and share some firsthand examples of this, but
Q: What are some key challenges in implementing machine learning algorithms for predictive maintenance in manufacturing and how do you address them from a technical standpoint.
So, see, we all understand the predictive analytics is transforming the manufacturing industry, it is enabling companies to anticipate and prevent equipment failures, optimizing the maintenance schedules reduce the downtime as I just talked about, right. But this has been made possible by building the machine learning models using historical data. These maintenance models beyond the typical business rules based conditional maintenance models can accurately forecast when a machine or component is likely to fail, thereby allowing for timely maintenance interventions by quality technicians on the shop floor.
So, this approach not only enhances the operational efficiency, but it extends the lifetime of our valuable assets like machines resulting in significant cost savings, machine uptime, reduced downtime etc. We just discussed about the variables you know, we typically use for building a machine learning model here. Now, coming to the challenges right, the development of the predictive and the prescriptive models, they involve the several key steps, we gather the data from sources that involves sensors, data maintenance logs, operational records, we process this data, we cleans standardize, enrich the data to ensure the accuracy and consistency. Then comes the feature engineering techniques to extract the meaningful features from this raw data. This serves as input to the machine learning algorithm. These algorithms are then trained on the data. And the goal is to learn the patterns and the relationships that can predict future failures or the maintenance needs. Now, the typical challenges what we usually face start with a data quality and availability. Most of the times we notice there is an incomplete noisy or inconsistent data that can hinder the performance of a machine learning model. Ensuring the availability of the high quality labeled data is very crucial for accurate predictions. Addressing this challenge often involves implementing robust data collection and validation processes as well as techniques for handling the missing or the erroneous data.
The other challenge we have seen is feature engineering, I mean extracting the meaningful features from the raw sensor data is very complex. It requires a domain expertise, it requires an understanding of the underlying physical process. Effective feature engineering is very essential for capturing the relevant patterns and improving the model performance. I will also talk about one more challenge on the imbalanced data. In many cases, failure events are relatively rare compared to normal operating conditions. And that leads to imbalanced datasets, it can cause a bias in the machine learning models towards the majority class. And that will result into the poor performance on the minority classes. Usually, we employ techniques like over sampling under sampling or class weight age to address the challenges. The other challenge I will talk about is interpretability. Right. While we can have the models which can achieve high predictive accuracy, it is a challenge to understand the reasons behind their predictions. interpretability is very crucial to building the trust in the system and enabling effective decision making. Usually, we employ the techniques like feature importance analysis, model visualization, use of interpretable models like decision trees to address these challenges. I will also talk about the scalability and the real time processing related challenges, right, we get a large amount of the data from multiple sources. It requires scalable and efficient processing pipelines to make timely maintenance decisions. So the distributed computing frameworks, streaming data processing, and cloud based solutions are usually leveraged to address these challenges. Moving on, you know, we all know the concept of data drift or concept drift, right. So it results into model degradation. Right, it may be because of the changing operating conditions, equipment degradation, or shifts in the underlying data distribution. So we need to continuously monitor and update our machine learning models to maintain their predictive accuracy. We typically employ techniques such as transfer learning model retraining strategies to help address these challenges. So from a combination of these robust data management practices, advanced feature engineering techniques, and application of appropriate machine learning algorithms and frameworks, we address these challenges. Once that model is implemented successfully, manufacturers can successfully implement the predictive maintenance or solutions, they can optimize their operations and they can maximize the value of their assets. As I said earlier, we have done multiple implementations at our manufacturing customers, we can be reached out for any further inputs.
Thank you, Rishi and Narsimha, you've dealt with this first time, like I said, and it would be great to hear from your experience,
Q: Can you share an example of a particularly challenging sale? You closed related to predictive maintenance and machine learning in manufacturing? What were the key obstacles you had to overcome?
Sure, Neerja. First of all, I fully agree with what Rishi has said, they are opportunities as well as challenges there, right. So let me put it into perspective by giving a real time example. See, one of the solutions I sold, particularly in predictive maintenance aspect is the life hub. Now, it's a solution based on analyzing the remaining life of a part. So in a manufacturing company, they manufacture multiple parts, right? Each part comes up with its own lifecycle. Now, as this part is being used, its lifecycle the originally lifecycle designated at the design time might vary. So it's important for customers to understand what is the remaining life that's what life hub does. So for example, we have deployed life up on a power plant OEM. Now, when it comes to power plant solutions, see these guys, they don't make money on an EPC contracts, their money is there on the services, they build two decades plus of service contracts, right, so their equipment is there on the field running on an energy production. Now taking right maintenance decisions with the help of LifeLock is helping them to save money and make more margins. It is also it also helped the power plant companies to take right decisions in terms of predictive maintenance. Now, we all know predictive maintenance means low cost, and it's compounded by doing remote analysis and selective maintenance you don't want to do same maintenance for all the parts you can do select to maintenance, but all this was not an easy sale at all. And prior to analysis, a few challenges that we have faced to one important thing is establishing business case. Now when it comes to energy companies, all the sales are already pre done power plant signs, a multi year service contract upfront, right, which should include all its digital solutions, everything. So when you go back and tell Hey, here is Life app that can save you more money, the customer is not ready to pay, because service is part of your contract already. So what we have done is we have built a business case with additional real time benefits. For example, in the original service contract, it says your parts have to be replaced by so on so date, now what life has does is life of taps into the real time usage, real time data of how the park is used, and it says, Hey, you can delay the service contract, you don't need to replace the park, you don't need a field engineer to go there and inspect it, it has been used, well, that already saves money. So that's one kind of cost benefit. So instead of replacement, sometimes with a small repair costs, you can just fulfill the needs or instead of repair just retrofitted. And then the whole part is secured. So that's where we built a business case and said these are all additional benefits. Second thing is data. Rishi has mentioned about this, right? There's tons of data out there. But what is important is all this historical data, how do you translate it into information? How do you build patterns? How do you use the engineering knowledge to convert this into insightful recommendations that are relevant to that company? Right, that is what life has was doing. So we spend a lot of effort converting this data into information and show to the customer that like, you know, Hey, these are insightful recommendations coming from your own algorithms and your own path. So you can safely take decisions around it, that helped the cause. But, you know, all good, we have the technology, we have the business case. But what was lacking there is in the market is finding the right people with knowledge. When it comes to manufacturing customers. These guys are running for 100 plus years, most of their Knowledge Hub is dotted with engineers who are like 50 plus years. And those engineers may not adequately understand the latest technologies like AI IoT. So finding the right to blend is always a challenge. So that's where we had to tap into the market, we went to across the geographies we found, we collaborated with engineering colleges, and we found knowledge in Europe and utilized them. That's how we sold the sales hub. See, there are opportunities, there are challenges, but finding the right experience is important. Now with companies like ours, Birlasoft, what we do is we bring best of the both worlds right? We bring experts from manufacturing companies, we bring people who are knowledgeable on latest technologies, and to do that system integration and to deliver use cases to come the large scale manufacturers.
Right. And Narasimha are looking ahead on that note, you know, what role do you see emerging technologies like AI and IoT playing in the future of predictive maintenance solutions for manufacturing companies?
Very bright future, let me start with that. See, look, traditional manufacturing companies made revenue out of selling parts components or whole products, as well as services. But you know, what is happening latest , data became a new source of revenue. Data, monetization is the real goal. Right now, I have seen in many manufacturing companies, they are carving out a digital vertical, they are designating Digital Officers to convert this data into information and insightful information and get some use cases out there and sell and develop new internal revenue streams. But one of the biggest challenge there is while the technologies are there, while there's tons of data because again, as I said earlier, manufacturing companies, most of them are operating for 100 plus years. There's a lot of data out there, but how to convert them into insightful information. While we have today, infrastructure like Cloud and doll which can pose and data lakes and all we can host all these data engineering analysis is the key thing. Right? And sometimes it's not humanly possible, that is where AI and IoT comes into the place right with AI, which is the self learning engine. And if these algorithms which have been developed for multiple years now, now is the right time to eat fruit out of them, right. So I say AI with that wrapped up interface UI or humanoid looking interface.
This is becoming very intuitive to us right now, this, this is opening up a whole world of possibilities for manufacturing customers, I will not even hesitate to say that possibilities are limited only by our imagination. I already see that right? smarter and autonomous missionaries are being designed and talked about machines performing human like tasks, like maintenance and repair. And even remote monitoring complementing it with, you know, robots who can do that remote monitoring, and AI engines who are doing that which are doing diagnosis is quite possible right now, Conducting virtual trainings, even in the area of trainings and simulations, you there are use cases being talked about. So once again, I want to sum it up saying we are at the right junction, we have credentials, manufacturing companies can utilize services from Birlasoft, and the possibilities are very bright.
Thank you, Narasimha that was very well put and very, very thorough. And, you know, if I were to ask each of you to sum up the key takeaway from this discussion in a sentence, what would you have to save Narasimha? Let's start with you.
Now is the right time, there are multiple opportunities out there, the possibilities are only limited by our imagination. That's how I would sum it up.
Yes, absolutely. And Rishi, what about you?
Well, I will say the predictive analytics is a big value add for the manufacturing customers, it is very important to collect the right data variables for the machine learning modeling. And it is very important for us to keep in mind the typical challenges we face in implementing machine learning models, and doing proactively ways to mitigate those risks coming up and reap the best benefits of developing these machine learning models. Yeah, that's it from my side.
Okay, well, this has been very in depth, which we truly appreciate. So thank you, Rishi, thank you so much for your time and thoughts on this. It was a pleasure speaking with you.
Yeah. pleasure speaking with you Neerja. Thanks a lot for your time too.
Well, that's a wrap, exploring some very interesting domains as always, that's what tech Lyceum is all about. I will catch you on the next one. Until then, it's me neerja signing off. Bye bye.