Birlasoft enables a cable manufacturer to achieve increased logistics efficiency with the 3D Load Configuration solution.
A leading cable manufacturer was facing challenges with optimizing truckloads of cable reels, which led to suboptimal logistical operations. The manufacturer did not utilize the container spaces effectively, and manually configuring truck loads led to unnecessary loading and unloading of items in multi-site delivery scenarios. This led to increased cost per delivery, delays in delivering items, and fines due to overloading of trucks.
The cable manufacturer partnered with Birlasoft to implement Oracle Transportation Management (OTM) as their primary transportation management system (TMS). The objective was to mitigate several transportation challenges with an automated TMS solution, along with OTM’s 3D load configuration to improve the loading efficiency. This enabled complete visibility into truckloads, maximized container space utilization, and lowered the cost per delivery.
Read the details of this engagement below.
The Challenge
#1. Suboptimal space utilization due to inefficient configuration of truckload
Optimizing truckload configuration in the cable manufacturing industry can prove challenging. Cable reels are cylindrical and vary in size and shape, making it difficult to place them optimally in truck containers. Moreover, cylindrical objects are prone to displacement when in transit. Therefore, it is necessary to secure them properly.
Additionally, some cable reels are very heavy, and as a result, the truckload configuration must be analyzed for stability. These factors made it difficult to identify the most optimal way to configure truckload while maximizing space utilization, directly impacting the shipment cost.
#2. Unwanted loading and unloading due to inability to account for delivery sequence
In multi-location shipments, the truckload configuration plays a key role in how efficiently the items pertaining to a shipment can be retrieved at the destination. Standard shipping containers typically open on one end. As a result, the last item to be loaded will be the first one out when unloading. This is also the case with truck loading ramps, where cable reels must be unloaded individually, following the Last In, First Out (LIFO) order.
The inability to account for the delivery sequence of shipments led to unnecessary loading and unloading at each site. This delayed the delivery process and added to the cost of deliveries while introducing the risk of handling-related damage.
#3. Overloading scenarios leading to fines and other transportation risks
Various routes have specific guidelines about the maximal permissible load on commercial vehicles. Due to a lack of visibility into the weight of the truckload, our client faced the risk of fines at checkpoints. Moreover, the inability to visualize the distribution of the truckload made it challenging to assess the stability of the container.
These challenges increased transport costs and made logistics workflows inefficient at our client’s organization.
The Solution
To mitigate the above challenges, the client engaged Birlasoft to empower the truckload configuration process with a suitable digital solution. Our team deployed the 3D Load Configuration capability of Oracle Transport Management (OTM) to help the planners configure and optimize truckloads.
#1. 3D visualization capability for configured truckloads
The 3D Load Configuration module of OTM enabled the planners to visualize the truckload from multiple angles. This enabled complete visibility into the truckload configuration and made the loading and unloading process highly efficient.
Moreover, visibility into truckload configuration also helped the planners assess the truckload for stability, distribution of multi-location shipments in the truckload, and understanding of stacking order and orientation of each item.
#2. Maximum space utilization with optimal load configuration
The deployed solution accepts the container dimensions and the shape, size, and weight of each piece of equipment to be shipped. Each truckload is optimized for maximum space utilization while following the delivery sequence and other loading rules using these parameters.
This results in a lower cost per shipment, effective utilization of fleet, and enhanced logistics KPIs.
#3. Efficient load configuration that accounts for dropping sequence
OTM 3D Load Configuration solution enables planners to map each item to multi-location shipments. Moreover, the solution takes the dropping shipment sequence as input and configures the truckload based on these parameters.
Ultimately, the configured truckload eliminates the need for unloading items that do not belong to a particular shipment. It follows the LIFO method to configure truckloads based on the dropping sequence, eliminating the risk of handling-related damage.
#4. Reduced risk of damage to goods with loading rules
Finally, the 3D Load Configuration solution allows planners to define loading rules. These rules include stacking preferences for each item, orientation constraints, and loading logic. It also enables planners to define truckloads based on handling rules for fragile items.
The solution outputs truckloads based on these parameters, which minimizes the risk of damage caused by handling and transit.
The Impact
The solution significantly enhanced the outcomes of logistics operations for the cable manufacturer. Here are some of the key benefits delivered by the solution.
1. Lower cost per shipment with optimal space utilization
The solution makes use of AI algorithms to optimize the configuration of the truckload. As a result, irregularly shaped items, like cylindrical cable reels are loaded in a manner which maximizes space utilization while accounting for other rules. This reduces wasted cargo space and lowers the cost per shipment.
2. Eliminated risks associated with truck overloading
The ability to infer the weight of each truckload from the load configuration eliminates the risk of overloading. Moreover, 3D visualization of the truckload assists in correct loading and helps planners assess the configuration for stability.
3. Increased loading and unloading efficiency
Accounting for the dropping sequence while configuring truckloads increased the loading and unloading efficiency. It eliminated the need for unloading items to retrieve other items belonging to a shipment, as the solution follows LIFO logic to configure truckloads.
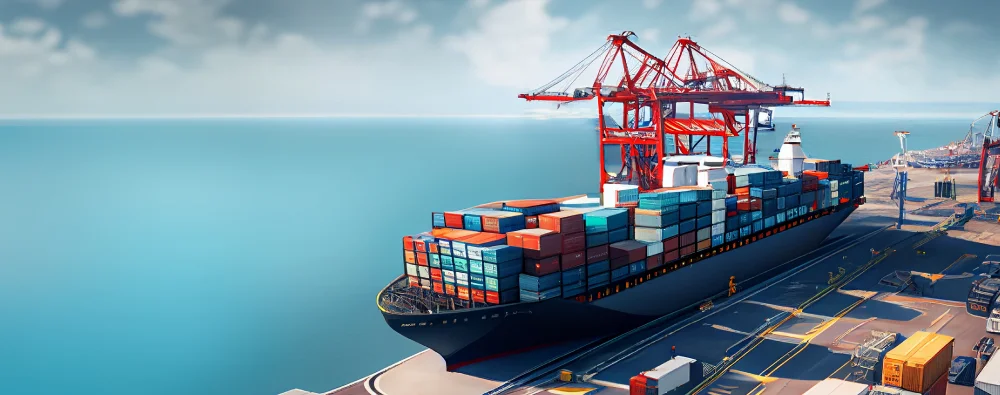
Meet Birlasoft at
the 2024 OTM User Conference Americas
the 2024 OTM User Conference Americas
August 4 – 7, 2024
Loews Hotel, Philadelphia, PA
Loews Hotel, Philadelphia, PA